Of the five orders of inside bend radii which one will suffer large amounts of springback without separating from the punch radius. In other words if youre bending 18 sheet use a tool with a 18 radius to form the inside of the bend.
How To Bend Sheet Metal 13 Steps With Pictures Wikihow
Clamp the wood on top of the metal to the workbench.
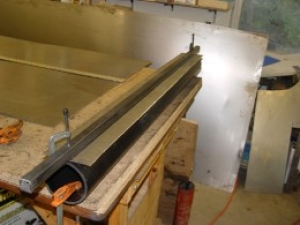
How to bend sheet metal. Step 1 Determine the angle at which you want to brake the metal and mark it on the protractor. Suppose B your desired bend angles complementary angle. This is necessary for the sheet to physically become bigger.
The brake will allow the user to bend the sheet metal in a continuous motion without any threat of getting warped away. Enter a Bend Radius if it is different from the default for the part. The semi-standard method allows us to change the interior inserts and to make different sizes of Z depending on each piece.
Heres a good rule of thumb for most materials. To bend sheet metal in a vice start by marking a line on the metal where you want to bend it. If youre bending 0020 thick material use a 0020 radius.
A brake is a device that allows you to bend a piece of sheet metal at a particular angle. Next place the wood parallel and slightly behind the bending line. And to measure the outside bend angles expansion knowing allowance is important.
Similar to other metal forming processes bending changes the shape of the work piece while the volume of material will remain the same. If you want a sharp 90 bend tap along the crease with a mallet. Monkeys Spinning Monkeys by Kevin Macleod.
It is important to keep in mind that there exists a central plane of metal near the center of thickness that remains unchanged no compression or stretching. Sheet metal bending is the plastic deformation of the work over an axis creating a change in the parts geometry. You can use a brake to attain the cleanest bends.
Simple sheet metal bender using a hand roller clamps and plywoodMusic. If your garage lacks this tool please purchase one from Amazon or the nearest store. If your sheet metal is long ask a friend to stabilize the part hanging out from the form blocks so it doesnt affect the bend.
It is important to make sure that the sheet is properly pushed onto the wipe die. When a piece of sheet metal is bent the inside radius material at the bend region is compressed while the outside radius material is stretched. We recommend a minimum bend radius of 1t for all sheet metal parts.
When it has reached the angle youre trying for release your pressure and remove the clamps. Z-shape metal sheet bending with different sizes. When air forming sheet metal you use the punch nose radius to calculate the bend allowance outside setback and the bend deduction.
In some cases bending may produce a small change in sheet thickness. When slotting sheet metal at the bend axis the materials average density in the bend region is decreased. The inside bend radius should be equal to the thickness of the material that youre forming.
With both hands pushing downward on the outer 2x2 begin bending the metal sheet applying equal downward pressure at both ends. There is no particular rule for how much the material should be weakened but as a rule of. As a result the wipe die also determines the bends inner radius.
Next put your wooden or metal form blocks in the vice and clamp your sheet of metal between the forms. The slack between the wipe die and the punch plays an important role in getting a good result. The sheet metal bending height should be at least 2 times the thickness of the sheet metal plus the bending radius that is H 2t R.
For example if the thickness of the sheet is 1 mm the minimum bend radius should be 1 mm. Add a double bend to a sheet metal face On the ribbon click Sheet Metal tab Create panel Bend. Thus the smallest radius of any bend in a sheet should be at least equal to the thickness of the sheet.
Finding the Bend Allowance. Metal shops have brakes mounted at different angles with automated braking arms however it is possible to bend sheet metal at home without the use of a brake. If you cannot afford a cheaper one dont worry.
Wipe bending or edge bending is another way to bend sheet metal edges. With this method we speed up the bending since from a single descent of press brake we make both bends at the same time. Finally bend the sheet up by hand to the angle desired.
Semi-standard tools 40ZP 40ZD. Select a model edge on each sheet metal face. Mark a bend line and place the sheet metal on the edge of your bench.
As shown in the figure below the sheet metal bending height is too low and the sheet metal is easily deformed and twisted when bent which makes it difficult to obtain the ideal part shape and ideal dimensional accuracy. Here a formula can help. The sheet metal bending techniques are supposed to help in warping sheet metal.
-
In other words it requires that a human life be killed. Here we will study the properties and examples of conservative and non-conservative...
-
These sacs mature and spread pollen. From Greek for two households. Male And Female Cannabis Grace Genetics Cannabis Seeds Flowers conta...
-
Features Climax Control Lubricant a clear lubricant with a special additive to help prevent premature ejaculation and help provide greater ...
quiz questions for women's day
50 International Women's Day Quiz Questions & Answers 2023 . 1 – Venus is the Roman Goddess of what? 2 – Name the Greek or Rom...

ads
Science Transition
Search This Blog
Blog Archive
- January 2023 (15)
- February 2022 (7)
- January 2022 (18)
- December 2021 (22)
- November 2021 (27)
- October 2021 (23)
- September 2021 (27)
- August 2021 (36)
- July 2021 (39)
- June 2021 (28)
- May 2021 (28)
- April 2021 (26)
- March 2021 (32)
- February 2021 (20)
- January 2021 (17)
- December 2020 (15)
- November 2020 (23)
- October 2020 (15)
- September 2020 (23)
- August 2020 (20)
- July 2020 (16)
- June 2020 (18)
- May 2020 (14)
- April 2020 (12)
- March 2020 (25)
- February 2020 (13)
- January 2020 (12)
- December 2019 (20)
- November 2019 (25)
- October 2019 (13)
- September 2019 (15)
- August 2019 (13)
- July 2019 (23)
- June 2019 (21)
- May 2019 (12)
Labels
- 1680
- 1984
- 2009
- 2022
- abcd
- about
- absolute
- accidents
- acid
- acidosis
- acls
- acoustic
- action
- activities
- acute
- adapter
- addams
- adhd
- administrator
- adopted
- adopting
- adults
- aesthetic
- affirmative
- afghanistan
- african
- after
- agenesis
- aggregate
- aggressive
- agitator
- aids
- airborne
- alcohol
- alle
- allen
- alpha
- alternative
- amendments
- america
- american
- amino
- amitiza
- amorphous
- anaesthesia
- analysis
- analytics
- analyze
- anatomy
- android
- anemia
- angelman
- answers
- antibody
- antifungals
- antiviral
- anxiety
- apache
- apnea
- apples
- archaeology
- area
- arthritis
- asbestos
- asia
- assay
- assessment
- asthma
- atlantic
- atrial
- attack
- attacks
- atypical
- audio
- auditor
- augmentation
- augmentative
- authentic
- autism
- autistic
- avatar
- average
- azole
- badminton
- baldness
- banking
- barnes
- barrier
- base
- based
- basic
- bass
- battery
- because
- become
- behavior
- below
- belt
- belts
- bend
- benefits
- benzoyl
- beside
- best
- better
- between
- beyond
- bible
- bibliotherapy
- biliary
- binge
- bipolar
- bitter
- black
- bladder
- blood
- body
- boiling
- bone
- book
- books
- booster
- bottom
- bowel
- brain
- brake
- bran
- branched
- bravecto
- breast
- brittle
- broaching
- bronchitis
- buddhism
- buddhist
- building
- bulk
- business
- cactus
- calcium
- calculate
- calculating
- calculator
- callosum
- came
- campaign
- canaan
- cancer
- cancri
- caps
- capsule
- capsules
- carbinol
- carbon
- carcinogen
- carcinoma
- cardiac
- care
- caring
- carlo
- carolina
- caskets
- caught
- causes
- cell
- cellphones
- cells
- center
- central
- ceramics
- cerebellum
- cervical
- chainsaw
- chance
- change
- characteristics
- charms
- chemical
- chestnut
- child
- childhood
- children
- chile
- china
- cholesterol
- chromosome
- chronic
- churches
- circle
- circuit
- cirrhosis
- city
- class
- clay
- clean
- cleansing
- clear
- clinic
- clinical
- clinicians
- clipboard
- cloud
- coaxial
- code
- coffee
- coins
- colitis
- college
- colon
- color
- coma
- comb
- comp
- companies
- company
- compare
- complex
- complications
- component
- comprehension
- compression
- computer
- computing
- concepts
- concrete
- condoms
- conflict
- conservative
- constant
- contact
- container
- contemporary
- contraction
- control
- conventions
- copper
- copyright
- core
- coronary
- cost
- costa
- counter
- cranial
- craters
- create
- creatinine
- credential
- credit
- criminal
- cross
- crst
- crystals
- culture
- current
- customer
- cutter
- cutting
- cycle
- cystic
- damage
- damascus
- danner
- data
- database
- dbms
- ddos
- dead
- debulking
- deceased
- decubitus
- deepwater
- deficiency
- define
- definition
- degeneration
- delay
- deletion
- delta
- dementia
- density
- design
- detox
- develop
- development
- developmental
- device
- devices
- diabetes
- diabetic
- diabetics
- diagnosed
- dialysis
- diet
- difference
- different
- diffuse
- digestive
- digital
- dinner
- disabilities
- disease
- disorder
- disorders
- distressed
- does
- dogs
- door
- dory
- download
- doxepin
- doxylamine
- draw
- dressing
- dried
- drinking
- drought
- drugs
- dutch
- dystocia
- dystrophy
- early
- earth
- earthquakes
- east
- ebook
- ecclesiastical
- echocardiography
- economics
- economy
- eczema
- edge
- education
- effects
- effexor
- egfr
- egypt
- ejaculation
- ejection
- elderly
- electrical
- electronic
- elementary
- elements
- elevated
- embassy
- emotive
- energy
- engine
- engineering
- engines
- english
- enlarged
- enteral
- environmental
- enzymes
- epidural
- epilepsy
- erythematosus
- esomeprazole
- esophagus
- estate
- esteem
- ethics
- ever
- evergreen
- everyday
- evidence
- evolution
- exam
- examples
- excellent
- exchange
- exercises
- expanded
- expectancy
- extract
- fact
- factors
- failure
- faith
- falls
- family
- fathead
- favors
- features
- feeding
- ferret
- ferrous
- fertilizer
- fetal
- fetus
- fibromyalgia
- fibrosis
- field
- finance
- find
- finding
- finger
- firms
- first
- fish
- fistulas
- flashes
- flea
- flight
- floor
- fluid
- flutter
- fontane
- food
- foods
- footed
- forensic
- forensics
- forest
- form
- formulation
- found
- foundation
- four
- fraction
- free
- freeze
- from
- frontieres
- full
- function
- functions
- fundamental
- funeral
- gait
- game
- games
- ganglion
- gangs
- garbage
- gatsby
- genders
- gene
- generalized
- generator
- george
- germs
- getting
- giant
- gifted
- ginseng
- gizzard
- glands
- glasgow
- global
- globe
- glutathione
- glycol
- gnawing
- gogh
- gold
- goleman
- good
- gospel
- gout
- grading
- graphite
- grass
- great
- greenleaf
- grip
- ground
- growth
- guns
- gyro
- hair
- hand
- handbook
- hands
- haney
- happy
- harness
- have
- hazards
- head
- headache
- health
- healthcare
- heart
- held
- helium
- hellp
- help
- hematopoietic
- hemodialysis
- hemorrhoids
- hepa
- hepatitis
- herpes
- high
- hilarious
- histiocytosis
- history
- histrionic
- holes
- home
- homeopathic
- hong
- horiba
- horizon
- hormone
- horse
- hospital
- hosting
- hour
- human
- humanism
- hunter
- hydrogen
- hypnosis
- hypoechoic
- identification
- identity
- immortal
- immune
- impact
- increases
- independence
- india
- indole
- infant
- infants
- infection
- information
- informative
- ingredient
- ingredients
- injection
- injections
- inositol
- input
- institute
- insulin
- integrating
- intelligence
- interest
- international
- interval
- interventions
- interview
- intestine
- into
- intrinsic
- invitation
- iron
- irritable
- isolation
- israel
- istat
- jack
- jane
- jersey
- jesus
- jewelry
- joaquin
- johns
- join
- journalists
- journey
- kerouac
- ketoacidosis
- ketogenic
- ketosis
- kidney
- kidneys
- kids
- kills
- kingdom
- knee
- knock
- kong
- korean
- labor
- labral
- lake
- laminate
- language
- languages
- large
- largest
- laser
- lasermax
- lasting
- lateral
- laws
- lead
- leadership
- leaf
- learners
- learning
- left
- leonardo
- lesions
- lessons
- letter
- level
- levels
- liberty
- license
- licensing
- life
- lifetime
- ligaments
- light
- lightweight
- likert
- limit
- line
- linseed
- lion
- liposuction
- liquid
- lisa
- list
- liver
- living
- location
- locations
- logical
- long
- loss
- lost
- love
- lower
- lowering
- lung
- lungs
- lupus
- lymph
- lymphoma
- machine
- machinery
- macular
- made
- magnesium
- magnetic
- make
- makeup
- male
- malformation
- malic
- management
- manipulatives
- mannose
- manufacturing
- many
- maoi
- marijuana
- marked
- market
- marketing
- mask
- massacre
- master
- material
- maternity
- math
- mathematical
- mathematics
- matter
- maturity
- maximum
- mayo
- mean
- meaning
- meanings
- measure
- measurement
- mechanism
- medecins
- medical
- medicated
- medications
- medicine
- medieval
- melanoma
- melatonin
- melon
- melting
- memory
- mental
- mesh
- metabolic
- metal
- metals
- meters
- metformin
- method
- mexico
- mice
- michigan
- migraine
- mild
- mind
- mining
- mirror
- mites
- mode
- model
- modeling
- models
- molding
- molecule
- monitor
- monitoring
- monsanto
- moon
- mortons
- motion
- motor
- mouth
- move
- movie
- mozzarella
- mulch
- multiplayer
- muscular
- myth
- nail
- nails
- names
- nasal
- national
- nations
- natural
- nausea
- near
- neck
- need
- needle
- negative
- neonate
- nervous
- neuroendocrine
- neuroma
- neuromuscular
- newborn
- nicotine
- night
- nightmares
- nist
- nitrates
- nitrogen
- nivolumab
- noble
- node
- nodes
- nodule
- noncommunicable
- noni
- normal
- nose
- nuclear
- number
- nursery
- nursing
- nutritional
- nutshell
- object
- ocean
- official
- ointment
- omega
- online
- only
- ophthalmic
- optimizing
- order
- organic
- organization
- organs
- orif
- origin
- orthopedic
- ourselves
- outdoor
- ovarian
- over
- overview
- oxford
- oxley
- pain
- painful
- painting
- palmer
- panels
- parents
- part
- partial
- particle
- particulate
- patch
- patches
- patent
- pathophysiology
- patient
- patients
- pear
- peel
- pellet
- pelvic
- penetrating
- pentahydrate
- people
- perception
- performance
- peritoneal
- person
- personality
- phase
- phosphate
- phosphorous
- phosphorus
- phrenic
- physical
- physiologic
- picture
- pictures
- pierce
- pine
- pizza
- plains
- plan
- plant
- plants
- plate
- pledge
- pneumonia
- poetry
- point
- polity
- poll
- pollution
- polycythemia
- polymyxin
- pontine
- position
- posture
- potassium
- pound
- powder
- power
- practice
- premature
- preschool
- preschoolers
- presentation
- pressure
- preterm
- prevalence
- prevention
- princeton
- principal
- principles
- problems
- process
- produced
- prognosis
- program
- project
- prolapsed
- prolonged
- proofs
- properties
- property
- prophylaxis
- prostate
- prosthetic
- protein
- provide
- pseudoscience
- psychological
- psychology
- public
- pueblo
- puerto
- pulmonary
- pulse
- puppies
- pylori
- quadricep
- queries
- questions
- quiz
- radar
- radical
- radiological
- rate
- ratio
- reading
- ready
- real
- reality
- reasoning
- recipe
- recipes
- recognition
- records
- recurrent
- recycled
- reduction
- reeds
- refugee
- rehab
- reinforcement
- relations
- relationship
- relativity
- religion
- remedies
- remeron
- removal
- renaissance
- renal
- repair
- replacement
- research
- resource
- respite
- restless
- restraint
- retina
- reversal
- review
- revolt
- revolution
- rfid
- rheumatoid
- rica
- rican
- rice
- rights
- ringing
- risk
- river
- role
- roman
- romantic
- room
- root
- roots
- roses
- rubber
- rules
- sacramento
- safe
- safety
- said
- sale
- salivary
- salmon
- sample
- sans
- satellite
- scale
- scared
- scenarios
- scheduling
- schizoaffective
- science
- scientific
- sclc
- screener
- screenplay
- search
- sects
- seizures
- self
- seminary
- seniors
- sensor
- sensory
- sentence
- sentinel
- sequencing
- server
- services
- severity
- shaken
- shaking
- shark
- sheath
- sheet
- shepard
- shipping
- short
- should
- shoulder
- side
- sided
- signal
- signs
- silicone
- sinuses
- size
- slavery
- sleep
- small
- smartphone
- smartphones
- smooth
- snapshot
- social
- sodium
- sodom
- software
- solar
- soluble
- soul
- source
- sources
- south
- soybeans
- spectrum
- speech
- speed
- sphere
- spill
- spills
- sponsor
- sports
- spray
- squamous
- stage
- stages
- stainless
- stalking
- stand
- standard
- star
- started
- starting
- state
- states
- statue
- steel
- stem
- step
- sterols
- stick
- stimulation
- sting
- store
- straight
- strength
- stress
- students
- study
- subliminal
- suites
- sulfate
- sulfuric
- summary
- supplies
- surgery
- surgical
- surveillance
- survive
- survivors
- sustained
- sweet
- symptom
- symptoms
- syndrome
- syria
- syringomyelia
- system
- systemic
- systems
- systolic
- tach
- tags
- tahitian
- tailbone
- target
- targeted
- teach
- teaching
- team
- tear
- techniques
- technology
- teenagers
- tendon
- term
- test
- testing
- tests
- texas
- that
- their
- theological
- theory
- therapy
- thermodynamics
- thin
- things
- three
- through
- thyroid
- tibia
- time
- title
- tomato
- tools
- topics
- tortuous
- toxic
- traceable
- tracking
- trafficking
- training
- transgenic
- translator
- transplant
- transportation
- treadmill
- treatment
- treatments
- tree
- trees
- trial
- triple
- trivia
- tropical
- troponin
- true
- tumor
- tumors
- turbinate
- tutorial
- twin
- type
- types
- ulcer
- understand
- underwater
- unit
- united
- universal
- university
- used
- using
- vacuum
- value
- vapor
- veins
- ventilation
- ventricular
- verses
- vertigo
- vinci
- violence
- virtual
- viscera
- vitamin
- vitamins
- voltage
- wake
- walgreens
- walls
- warfarin
- warts
- wash
- washer
- washington
- water
- waveguide
- weapons
- wechsler
- weed
- weight
- west
- what
- when
- where
- while
- white
- wide
- will
- williams
- witchcraft
- with
- withdrawal
- without
- women
- word
- words
- work
- workplace
- world
- worse
- wort
- wounds
- wrist
- writing
- yellow
- york
- zometa